Self-healing material for improving air traffic safety
- Dr. Sravendra Rana
- Published 07/07/2022
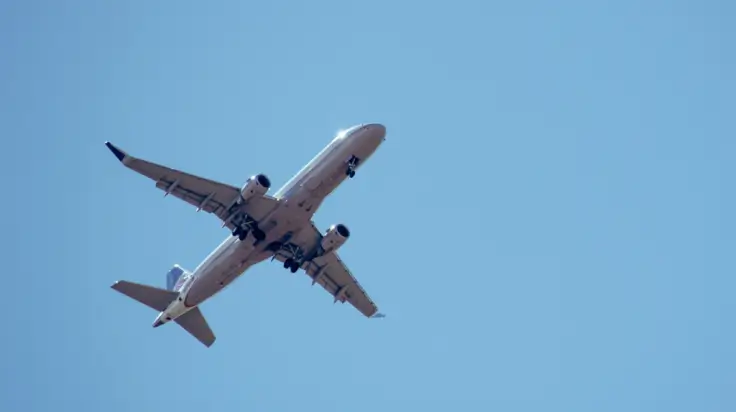
Image credit: Pexels
There is a growing demand for recyclable and healable composite material in the automobile and aerospace industry. The material has great mechanical strength, and has applications in the development of high-class resins to make aircraft components more durable
Self-healing material is inspired by Nature – the way natural healing of wounds and cuts occur in living species. In the case of structural material, long-time degradation gives rise to microcracks, thus, causing material failure. Therefore, conventional thermosetting material is susceptible to failure after fracture or damage during service, leading to a sharp decrease in their safety and lifespan. The exploration of recyclable and healable thermosetting polymeric material is in high demand as it would allow to overcome not only difficulties connected to damage diagnosis, but also include appropriate interventions to restore (and subsequently) recycle the material functionality. Different concepts to generate material that are able to repair autonomically or via an external stimuli, such as heat, light, or pressure, have been designed through various approaches such as capsule-based covalent systems, where catalyst cost, stability and processing is still a challenge.
A project funded by Science and Engineering Research Board (SERB), seeks to investigate the development of fiber-reinforced self-healing composite materials for aerospace applications, where small cracks, which are caused by stress, should be able to “repair” at low temperature. In order to match the industrial importance, enhancement of mechanical strength without sacrificing the bond exchange capability still limit their real-life application, however, these limitations can be overcome through the development of fiber-reinforced self-healing composites. This is to ensure more safety in air traffic and to make aircraft components more durable.
Two different strategies are executed to prepare the self-healing composites, where the first concept works with polymers whose molecular chains are automatically interrelated after a crack in the material, and this happens without mechanical intervention from the outside or an elevated temperature. For use in aircraft components, however, this reaction must also be carried out at lower temperatures so that even minor damage can be remedied during the flight. The second concept involves vitrimers (a material that exhibits a thermoset polymer like mechanical properties/ durability and thermoplastic like malleability/ processability). In other words, vitrimers have combined advantages of both thermoset and thermoplastics polymers. Due to their associative dynamic covalent adaptive networks, vitrimers can reform their cleaved bonds rapidly without failure. The associative dynamic covalent adaptive network exchange behavior of vitrimers allows their reprocessing/recycling in most of the performed material. Given the huge amount of unrecyclable waste from thermoset polymer-based products, the potential of the vitrimer concept is highly attractive, which meets the recently increasing demand to create polymers with efficient recyclability, together with the need to reduce CO2-emission and petroleum resources consumption.
The combination of the above strategies can be valuable, considering the increasing demand for recyclable and healable composite material with great mechanical strength, especially for the future development of high-class resins in the automobile and aerospace industry.
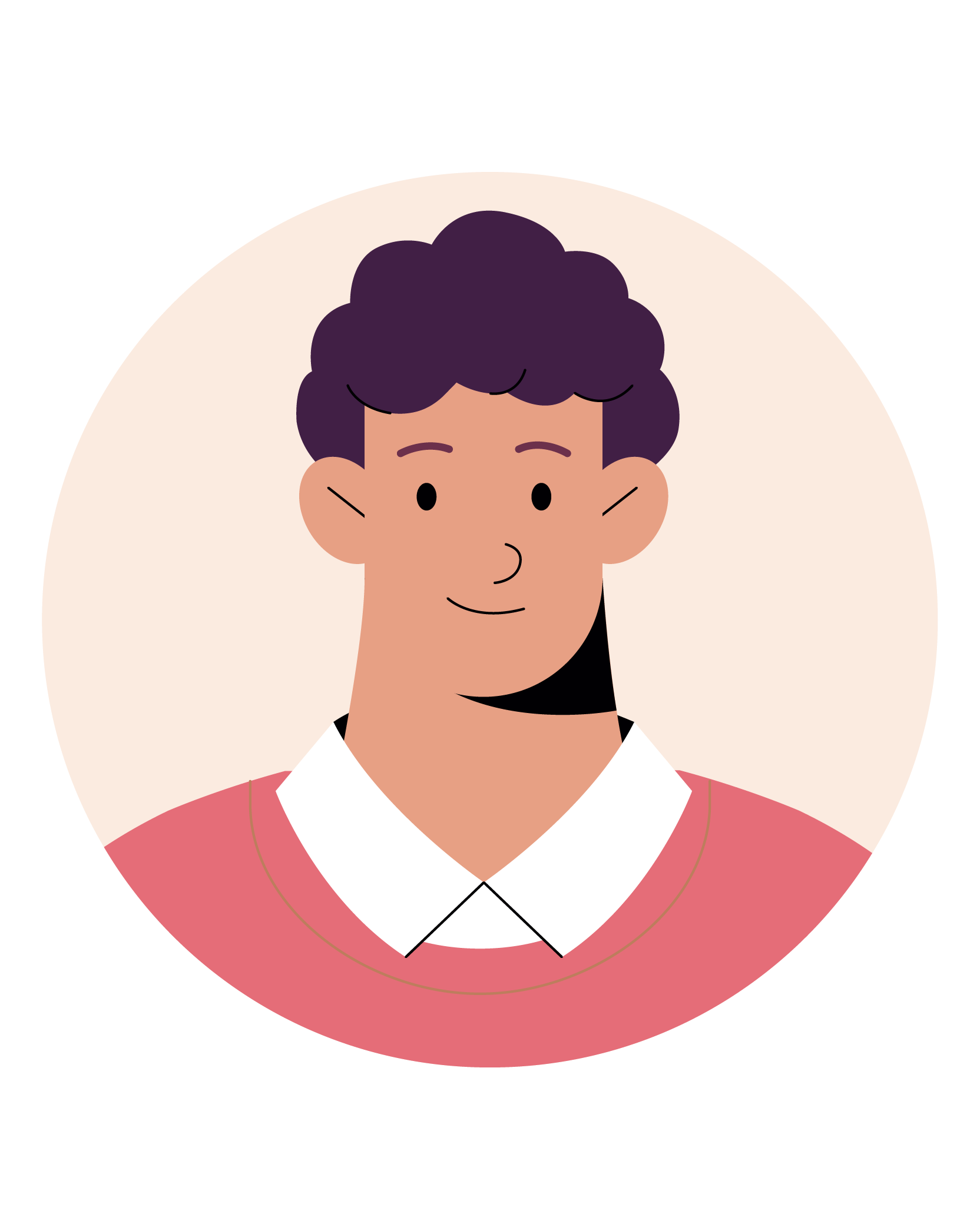
Dr. Sravendra Rana
The writer is Dr. Sravendra Rana, Professor, Applied Science, UPES School of Advanced Engineering
Tags
- Faculty
- Research and Innovation
- School of Engineering
UPES Admission Enquiry
Subscribe to UPES Blogs
Join our community for exclusive stories, insights, and updates
By clicking the "Subscribe" button, I agree and accept the privacy policy of UPES.